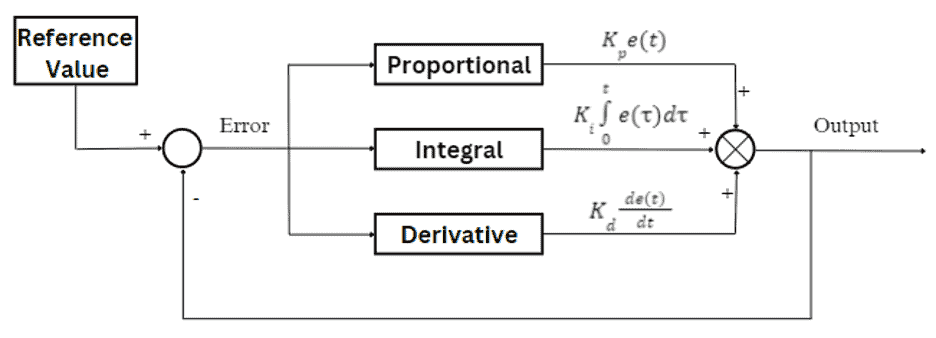
MPC vs PID – A Comprehensive Control Method Comparison
Control systems play a crucial role in various industrial processes by ensuring stability, efficiency, and optimal performance. Among the myriad of control methods available, Model Predictive Control (MPC) vs Proportional-Integral-Derivative (PID) stand out as two competing strategies. In this article, we delve into the intricacies of each method, compare its strengths and weaknesses, explore applications, and provide insights on selecting the most suitable approach.
Model Predictive Control
Model Predictive Control is a sophisticated control strategy that leverages a predictive model of a system to make decisions about the control output. It calculates the optimal control action by minimizing a ‘cost function’, which can be likened to the ‘error’ in PID control. Because of the predictive nature of the MPC, it is ideal for systems with complex dynamics and varying operating conditions. The main features of MPC are the process model and optimization.
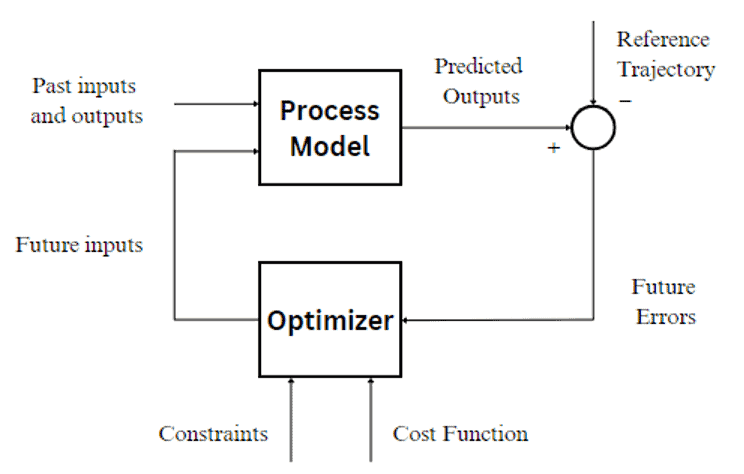
Process Model
This refers to the mathematical model that the system uses to predict future behavior. Often, it is derived from an algorithm unique to the system being controlled or from established first-principle equations. The model incorporates information about the system’s dynamics including past inputs, past outputs, and even future inputs in predicting an output to the controller. It keeps repeating this process until the desired output is achieved.
Optimization
The optimization feature of the MPC is targeted at finding the best control signal. After each time step or prediction from the process model, the optimizer takes into account the future errors, which is obtained by comparing the predicted output to the reference trajectory of the process. Moreover, the optimizer also considers the defined cost function and constraints as it solves the problem to produce future control outputs.
These outputs are still fed back to the process model and used in generating subsequent predicted outputs. This continuous exchange between the process model and optimizer enables the recalculation of the optimal control actions in real-time. As a result, the MPC adapts to changes in system dynamics and operating conditions, which makes it effective for systems with variable parameters or nonlinear behavior.
Benefits of MPC
The MPC provides several advantages including:
- Ability to control a system at both supervisory and local loop levels.
- Can cope with slow-moving processes with time delay. Also, it handles time-varying dynamics.
- It is the ideal control strategy for handling constraints and uncertainties due to its anticipatory control actions.
- Provides an easy method to integrate energy conservation strategies in the controller formulation.
Drawbacks of MPC
- The predictive nature of MPC involves solving optimization problems at each time step, thus, leading to higher computational demands.
- Implementing MPC requires a good understanding of system dynamics and model accuracy, which is difficult in certain applications.
- MPC often requires a large number of model coefficients to describe a response.
Applications of MPC Control
- Chemical Processes: The use of MPC is common in the control of chemical reactors and processes where precise control is crucial.
- Automotive Systems: Vehicle control systems, optimizing fuel consumption, and improving overall performance of automotive systems typically involves MPC deployment.
PID
As the most widely used control strategy, Proportional-Integral-Derivative control has proven to be a big advantage in industry. The basic idea of this control method is to adjust the output of a system based on the error, which is the difference between the setpoint and the measured output. Simply put, the PID uses the previous and current state of a system to determine an appropriate controller output. It achieves this using three parameters which are the proportional, integral, and derivative.

Basic Parameters of PID
- Proportional: The proportional parameter takes into consideration the current error in the system, which is the difference between the desired setpoint and the actual system output. Based on this current error, the controller in the system provides a response to minimize it.
- Integral: The function of the integral parameter is to accumulate the past errors over time, thus, eliminating steady-state errors. This covers up for the proportional parameter’s inability to account for long-term deviations from the setpoint.
- Derivative: The derivative term anticipates future errors by considering the rate of change of the error. As a result, it helps dampen the system’s response and improve stability. This is especially useful in systems that are prone to overshooting or oscillations.
With these three parameters working together in the system, the final control output, u(t), is a sum of the proportional, integral, and derivative terms. As the controller output is adjusted based on the current error, past errors, and the predicted future error trend.
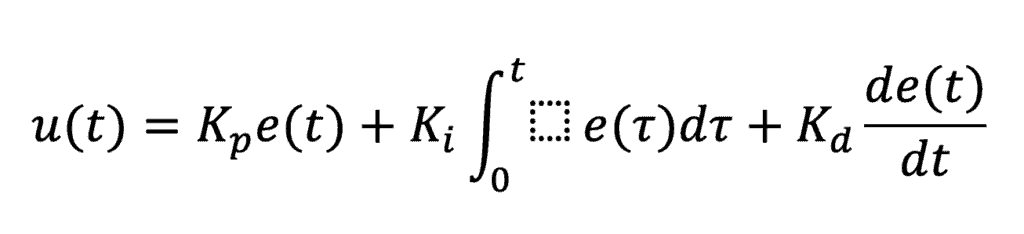
Advantages of PID Control
PID control enjoys wide adoption in industry because of the following benefits:
- The implementation and tuning of PID control are straightforward, which makes it suitable for several applications.
- It offers good stability in many linear and near-linear systems.
- This control strategy is robust in dealing with uncertainties and variations in system parameters.
Disadvantages of PID Control
- PID controllers usually struggle when dealing with highly nonlinear systems and processes with significant changes in dynamics.
- Attaining optimal performance often requires careful tuning, which can be time-consuming.
Applications of PID
- Temperature Control: PID controllers are popular in heating, ventilation, and air conditioning systems to maintain desired temperatures.
- Motion Control: Applications such as robotics and automation for precise motion and position control often deploy PID controllers.
Selecting the Best Control Method
Choosing between MPC vs PID depends on the specific characteristics of the system and control requirements. For systems with complex dynamics, varying operating conditions, and stringent performance requirements, MPC is the go-to option. Moreover, the MPC excels in systems with multiple disturbance variables, and multiple constraints. On the other hand, for simpler systems with well-defined dynamics and ease of implementation, PID control suffices.